It all started without a name
Introducing any new product is a special event and we gave our first Zultan cymbals a special launch at the beginning of the third millennium. Naked, you could say. Still without a brand or product name, we presented our first cymbals in Frankfurt, Germany, at the world’s largest trade fair for musical instruments at that time.
To ensuring that nothing would prejudice the drummers who gave their opinions on sound and quality, we decided to keep the origin and maker of our cymbals a secret.
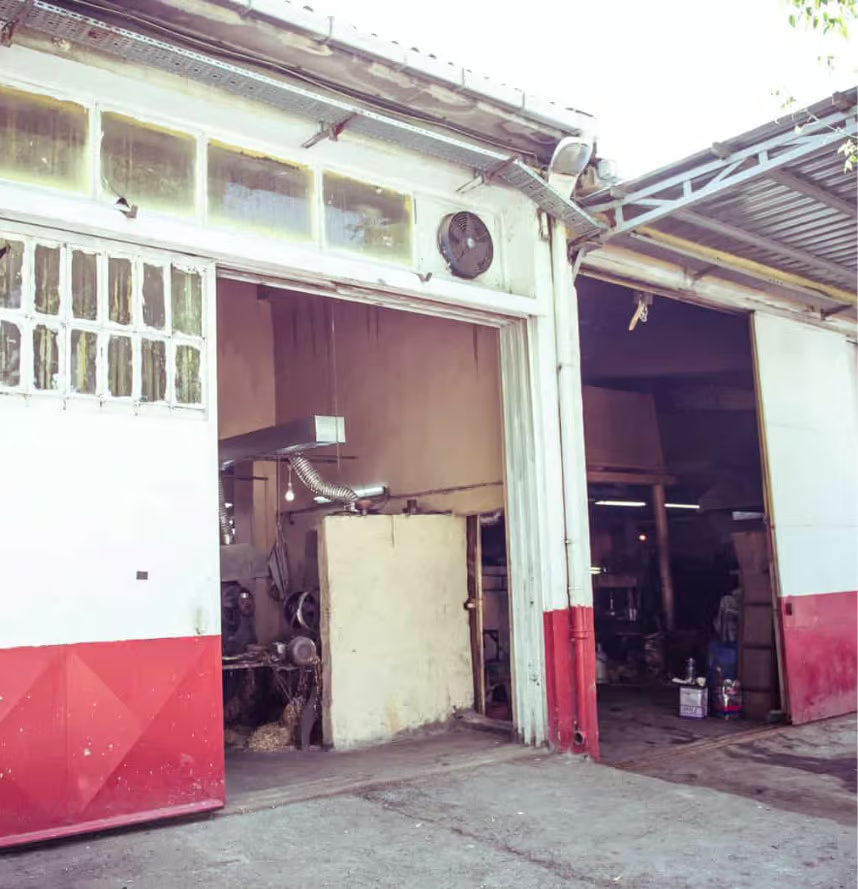
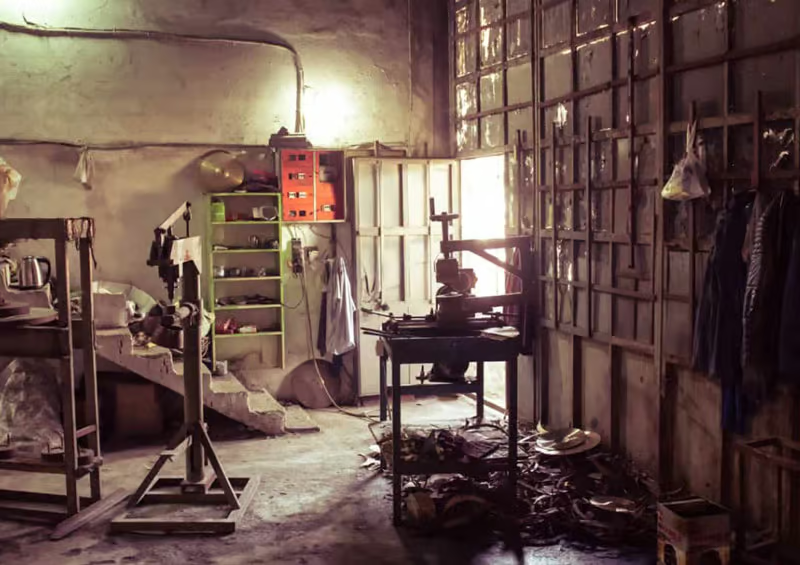
Thankfully, the response was positive across the board. Even disregarding their price point, these cymbals held their own in terms of finishing, quality and sound when compared to cymbals by renowned makers.
That was the first chapter of the Zultan story, written before our cymbals even had a brand name.